Most purveyors of hardwood flooring are retailers who purchase their flooring from wholesalers who purchase it from the mills that produce it. The retailers may brand the product as their own, but it’s likely the same product moving up the supply chain to showrooms and websites of numerous other retailers. And it’s a product that those retailers likely have little control over when it comes to its quality.
That’s why Vermont Plank Flooring stands out from the wood flooring pack. We mill all of our own floors right at our Brattleboro, VT headquarters. By doing so, we can exert our exacting standards through every step of the process, and we can create flooring specific to each customer’s tastes and demands.
The craftspeople who staff our mill are part of the Vermont Plank Flooring family. They’ve been trained to create excellence, and they do their work with conscientiousness and pride. They work diligently to produce and deliver the finest wide-plank hardwood flooring found anywhere, compelled by the fact that the name on the order is a real customer, a real family, not a faceless retailer or big box store.
When we say flooring planks are custom milled for the customer, we mean it! All of the flooring we produce for each order is processed as a batch at each station before being moved to the next, because each machine is calibrated to that customer’s specifications, and each plank is checked every step of the way to assure it meets those specifications.
If you are considering Vermont Plank Flooring for your project, please come visit us! We’ll be happy to bring you into the mill to see the process first-hand and to meet the fine people who’ll be crafting your floor. In the interim, here’s a peek at the process.
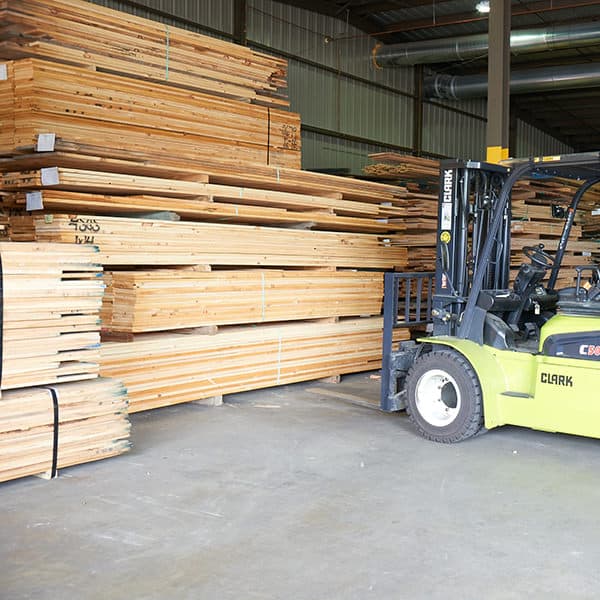
Raw Lumber Arrives
Our wood comes from sustainably managed forests primarily in Vermont, New Hampshire, and neighboring northeastern states. After being harvested, the trees are trucked to nearby sawmills where they are milled into rough planks. Because we demand that only fully mature, healthy trees are harvested, the planks we receive are two-to-three times wider and longer than the industry standards – up to 12–19 inches in width and 10–16 feet in length, depending on the species. These 1-inch thick planks are dried in kilns at the mill before being loaded onto trucks for the trip to Vermont Plank Flooring.
Upon arrival, we immediately move the raw lumber by forklift from the truck into our indoor storage area, so it doesn’t spend anytime outside exposed to the elements. It is graded for quality and prepped — select grade cherry is separated from character grade cherry, for example — and immediately tagged with the name of the customer for whom it is intended. There the boards wait in the queue until that customer’s order is scheduled for production.
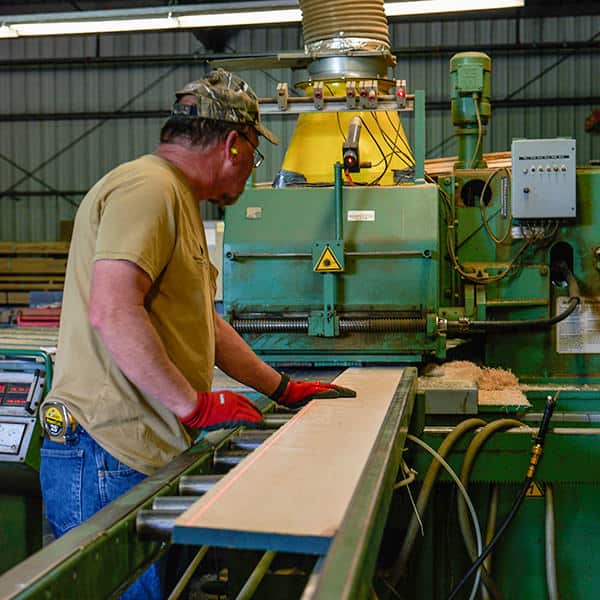
Ripping and Pre-Planing
The production process begins at the gang rip saw, where we "rip" (meaning, cut parallel to the grain of the wood) the rough-cut planks to width, and ensure that the long edges are absolutely parallel with one another. The saw has multiple blades, enabling it to cut planks at four different widths in one pass. Laser beams guide the process for perfection. The off-cuts are ground into sawdust on-site and then sold to a wood pellet producer, thereby minimizing waste. We then meticulously measure to ensure that all planks for that specific project are exactly the same width.
The planks are then passed through a planer for the first time. A planer removes material from the surface of the board to reduce its thickness. We pre-plane solid hardwood planks to 15/16ths of an inch, and boards destined to become engineered planks to a thickness of 22 millimeters. Our planer can accommodate boards up to 20 inches in width. Depending on the project, the boards are then moved either to the main workroom next door (for solid wood plank orders), or just beyond that to the lamella room (for engineered plank orders).
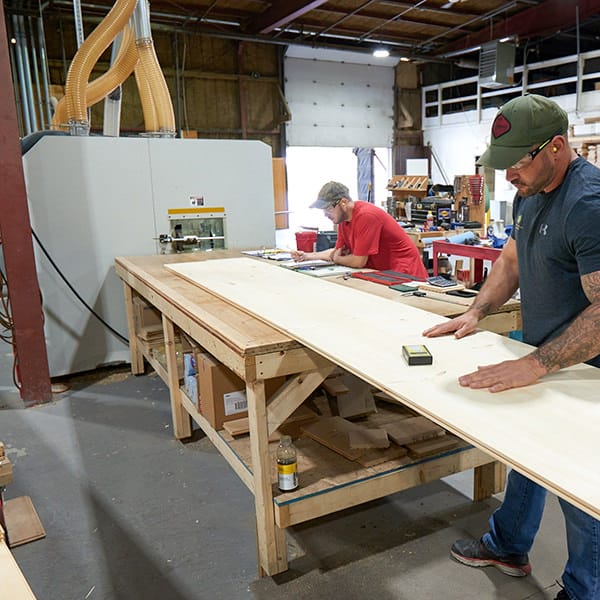
Molding, Removing Defects, and End-Matching
For a solid hardwood order, the molder is the next step of the process. Here at the molder machine, a lot of mechanical magic – along with a lot of technical know-how – is on display. The preplaned board goes in on one end, and a beautifully smooth plank emerges from the other end at its final thickness of 3/4 of an inch. Additionally, the bottom of the plank will now have a series of long shallow grooves called stress reliefs running from end to end. These help prevent the plank from cupping when it is later subjected to humidity variations. But that’s not all. The molder also mills the precision tongue and groove along the long sides of the plank.
The planks then move to the end matcher, which like the molder, is also a multi-tasker. First, each plank goes through a defect check in which flaws, large knots, and other serious imperfections are marked by hand in bright orange fluorescent chalk. The saw reads those marks as the board is fed through the machine, automatically removing the flaw by cutting the plank on either side of the imperfection. This is why custom planks won’t all be the same length. Some planks will make it through the inspection virtually unmarked, resulting in one very long plank, and others will require more substantial trimming, leading to two or more somewhat shorter planks. After cutting the planks to length, the end matcher then mills the tongue and groove along each of those freshly cut plank ends.
The craftsman at this station then performs a series of quality control checks – measuring, fit-testing, and performing some critical record keeping.
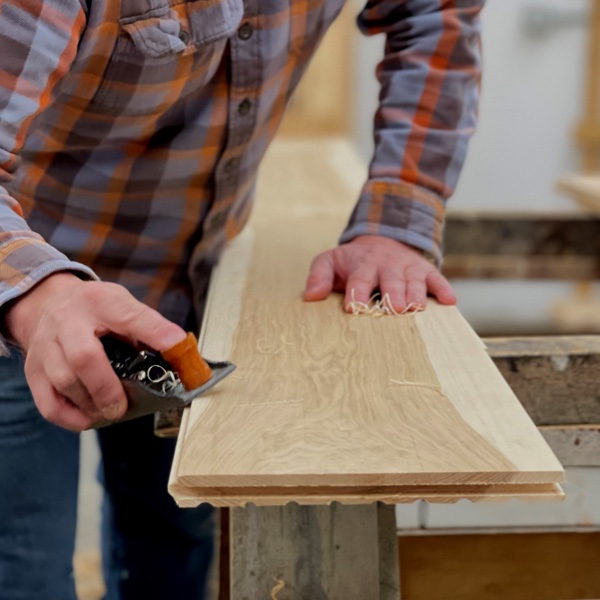
Optional Treatments
At this point in the solid hardwood process, the planks go in different directions depending on the specific order. About 50 percent of our clients order planks that are unfinished – to be sanded and finished on-site once they are installed. These orders head to the packaging area. The other 50 percent are prefinished at our mill. For these customers, we then run the planks through a double head sander to create the optimal smooth surface for receiving the desired finish treatment. A small number of clients instead request the opposite: a weathered, antique look. In these instances we run the planks through a wire brusher, which scrapes a texture into the face of the board, bringing out the natural grain, or to enable a dramatic “white-washed” effect.
These boards are then moved to the finishing shop. But before looking in on the finishing process, we need to go back and see what's happening to the boards destined to become engineered planks.
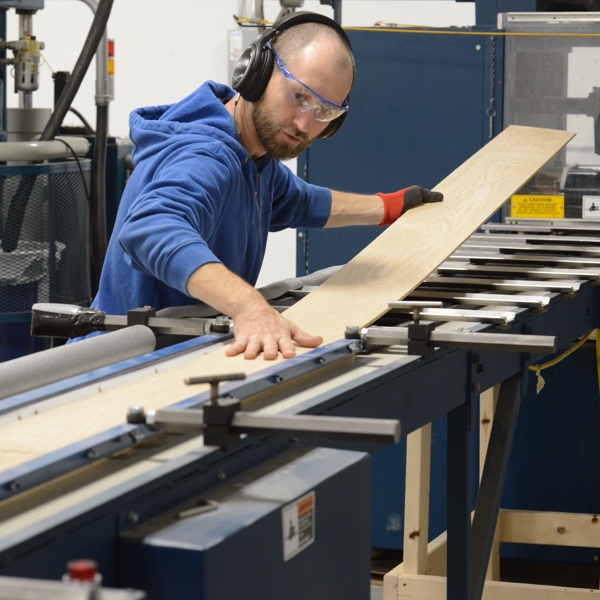
The Engineered Plank Process
Engineered planks are made of a top layer (called a lamella) of hardwood, fixed to a cabinet-grade plywood base. This Zero-Added-VOC process exceeds CARB 2 standards and is done entirely in-house at our solar-powered mill in Brattleboro, VT. Because of the fabrication process, the maximum width of our engineered wood flooring is 12 inches.
Learn more about our Engineered Wood Flooring on our dedicated page here.
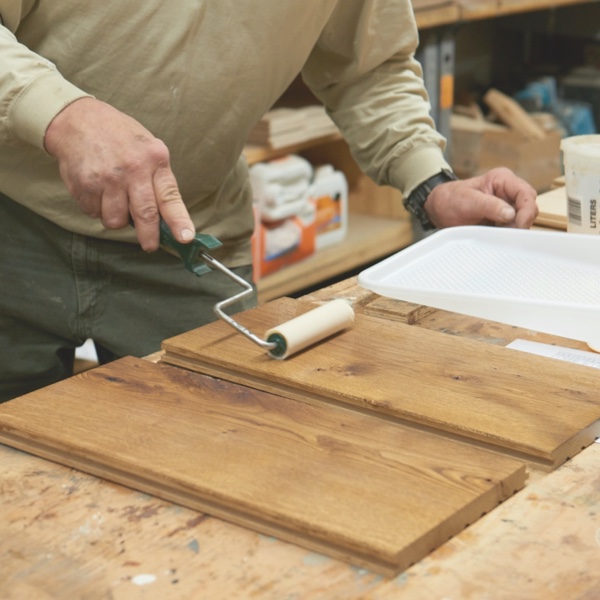
Finishing
For customers who choose to have their floors prefinished, the planks, whether solid hardwood or engineered, are brought to the Finishing Shop adjacent to the mill. There the boards are prepped, with any small remaining character issues resolved with a touch of wood putty and a light hand sanding. Then the finish crew begins applying the finish - either a beautiful selection from one of our Species Collections or a custom formula developed in consultation with the customer.
The finish is applied by hand with either pads, rollers, buffers, or lint-free cloth, depending on the choice of finish material – most often water-borne urethane, tongue oil or other natural oils, or hard wax, mixed with a variety of tints, stains, and pigments. The finish is generally applied in 2–4 coats with a light sanding between each application.
Read more about our Custom Sample Shop and Finishing Process below.
Clients with large commercial projects (floors destined for shopping malls, hotels, etc) can learn more about our UV-Cured Aluminum Oxide finishing options here.

Packaging and Shipping
With the production and finishing process complete, each order is carefully stacked on pallets, labeled with the customer’s name, address, and delivery notes for the trip, and then wrapped for shipment. Our packaging process takes into consideration the worst-case scenario. This is Vermont – New Englanders understand all kinds of weather conditions! We go to great lengths to protect the flooring from damage that can occur while in transit and from exposure to moisture. Orders are shrink-wrapped by hand (no fancy shrink-wrapping machinery involved) and then banded to the pallets. Finally, when the transport truck arrives from the common carrier, we carefully forklift it into place and wave adieu as it heads off to a long life beneath a family’s feet.
When you order samples from us—because you'd like us to try to duplicate a wood finish that's already in your home, or you want to see how an Ebony finish looks on Eastern White Pine— our Artisan Finishers will create it for you. Jay, pictured below, is a genuine master at translating your vision into reality.
We encourage you to schedule an appointment to visit us here in Brattleboro and see our finishers at work. Better yet, plan on spending some time and challenge us to create the perfect finish sample that matches—or exceeds—your ideal floor vision!
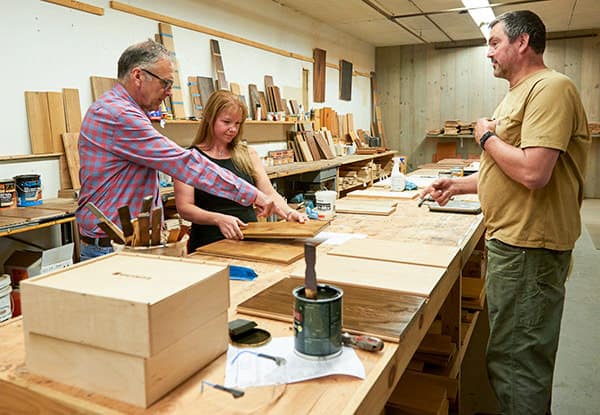
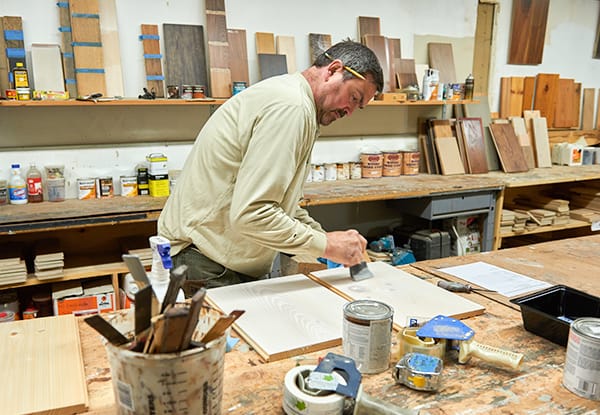
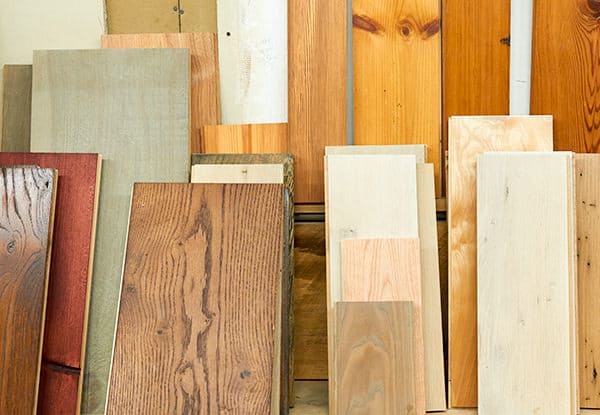
Sustainability
Read about VTPF's commitment to the environment